Rainscreen & cladding, Masonry
Waterhouse Gardens
The project
Located in the heart of Manchester’s city centre, Waterhouse Gardens is an exciting mixed-use development being built on the historic former Boddington Brewery site. Its namesake is homage to the architect Alfred Waterhouse, designer of Manchester Town Hall and the nearby prison with its landmark Grade II listed ventilation tower constructed in brick and sandstone. This vibrant new neighbourhood has been meticulously planned to create a community for residents looking for the modern city centre lifestyle. When finished, the project will provide 556 high quality homes, luxury amenities, and 31,000 sq.ft of commercial and retail opportunities, set across five towers ranging from 10 to 26 storeys.
Details
Year
Completion Q2 2026
Location
Manchester, UK
Building use
Residential I Mixed
Developer
Salboy
Main contractor
Domis Construction
Brickwork contractor
Kinlan Brickwork Ltd
Rainscreen contractor
LDG Contracts
Products used
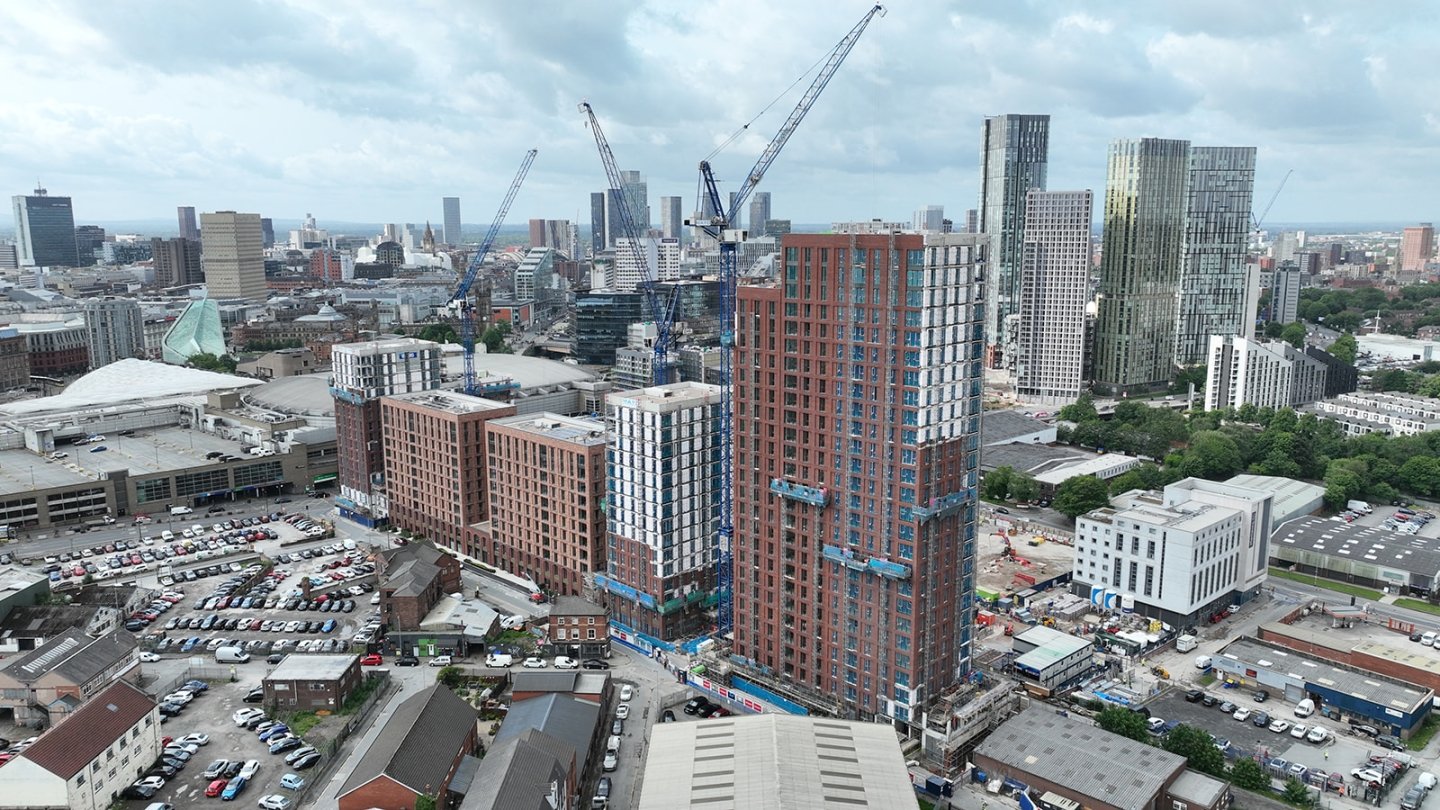
Design and specification
The elevations of each tower predominantly features a traditional brick finish, echoing the historic red brick brewery buildings that previously occupied the site to create a timeless aesthetic that sets this modern urban development firmly within Manchester’s varied architectural landscape. The towers are joined with decorative rainscreen elements to create a sense of cohesion across the site.
Siderise were brought in by Domis early in the design phase to address the passive fire protection and drainage requirements for the masonry wall elements. With a fire performance requirement for 2-hour fire resistance on all towers, we recommended a combination of EW Cavity Barrier and Firestop and CT Cavity Tray, which work together hand in hand.
This systemised approach provides continuous fire stopping and effective moisture management sourced from a single supplier to ensure complete compatibility. Additionally, the Lamella insulation core of the EW Cavity Barriers enables them to be friction-fitted within the cavity to wet brickwork without compromising the stability of the wall structure, helping yield significant advantages in build program speed and sequencing. It also allows for the cavity barrier to be fully penetrated by masonry supports, whilst maintaining its fire resistance. Incorporating these into the design from the outset, and having the benefit of full masonry support penetration, helped to save significant money and time, as the team could omit including concrete up- and down-stands from the slab edge.
Furthermore, Waterhouse Gardens was the first project to have our newly launched RH25-120/120 Horizontal Cavity Barrier, which was installed by LDG Contracts after the fire performance specification for the rainscreen element was changed from 90-minutes to two-hours by the project team.
“Using Siderise on the scheme has been a great success. We’ve incorporated their new 120/120 fire barrier into our rainscreen cladding system. Their excellent service and site support have been key in ensuring a smooth installation on what has been a very exciting project”.
Demi Mulvanny, Operations Manager, LDG Contracts
Throughout the project the Domis design team had been developing their own set of standard details to make life onsite easier on both this and future projects. To ensure that the passive fire protection elements are properly addressed, they have been working closely with Siderise Technical Services, drawing on our own standard details and test data, and asking advice on what is possible.
Installation and inspection
Due to the volume of product needed on this large site, the cavity barriers were supplied to site in slab form and then cut to size to fit the specified depth by Kinlan’s expert team in a dedicated workshop on the site. This helped to reduce onsite wastage, maintain quality standards and enabled a continuous supply of product, when and where the bricklayers needed it.
Siderise Site Services have provided ongoing support throughout the construction phase. This included delivering Product Information Training and ongoing site visits to provide detailing advice and inspections to check the installation was progressing as intended. This continual correspondence allowed any issues, particularly relating to the interfacing of the products, to be rectified early in the build programme ensuring a consistent quality level across the large development. Additionally, in between visits, the installation team at Kinlan were able to self-audit their work via the Siderise Inspection App.
“I think having that onsite inspection team is critical. One reason is we can get our standard details put in and checked to make sure that all the other teams and consultants are installing things in the right way— giving us peace of mind. But, invariably, we always come across bespoke details— something happens on site and we have to think on our feet.
Having the robust test data and certificates for all the different products from Siderise, and the fact they have been tested together, means we know they are compatible.”
Richard Scott, Design Manager, Domis
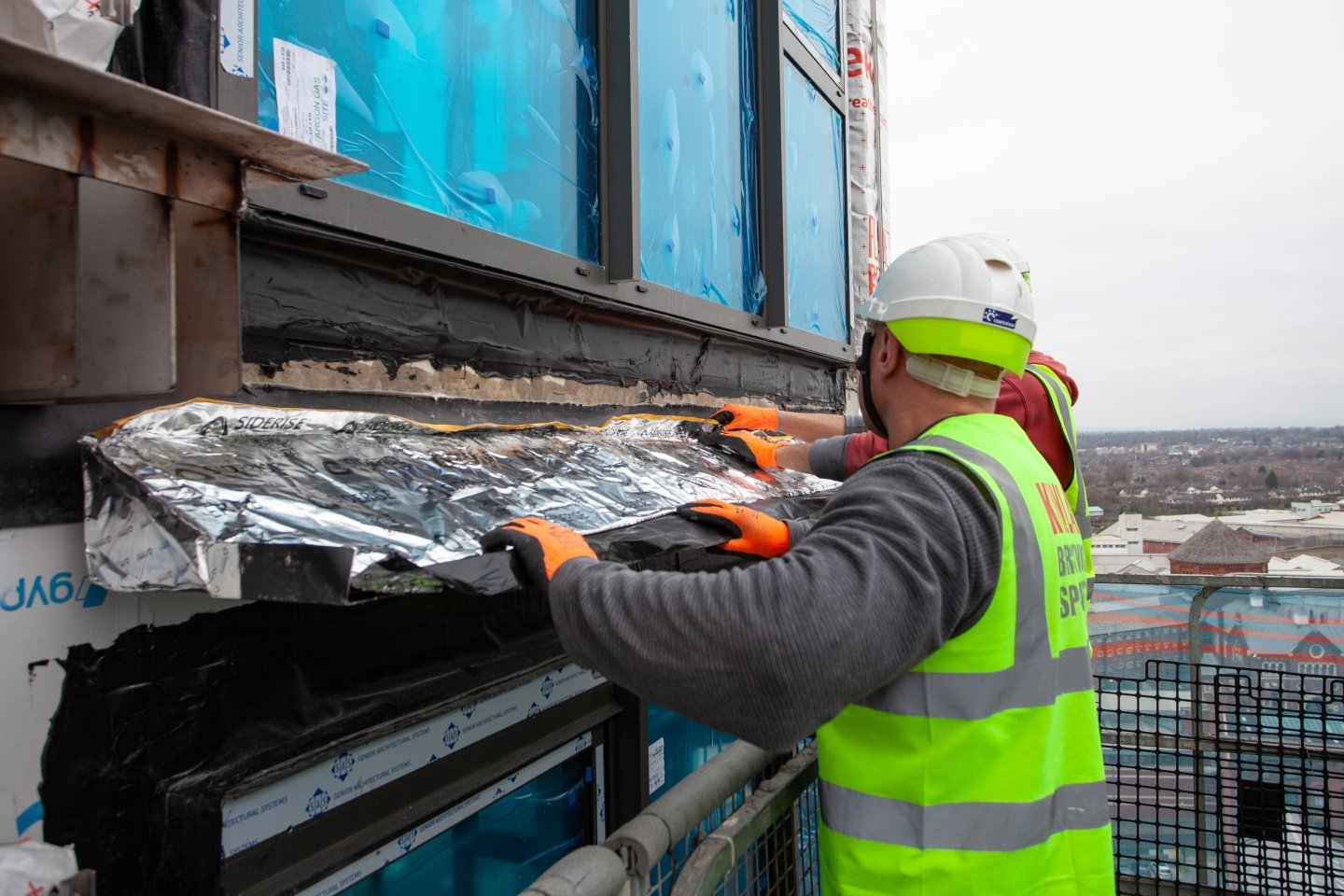
Summary
Waterhouse Gardens is bringing the buzz and energy back to the former brewery site, transforming it into a vibrant community for the next generation of city centre dwellers to thrive. This past-meets-future story is echoed in the relationship between Siderise and the Domis and Kinlan teams. Drawing together our knowledge and experience, we have been able to develop a high level of quality and understanding which can be applied to future projects, from developing standard details to helping to upskill the installation team. This will help to ensure the creation of safe, compliant developments for many years to come.
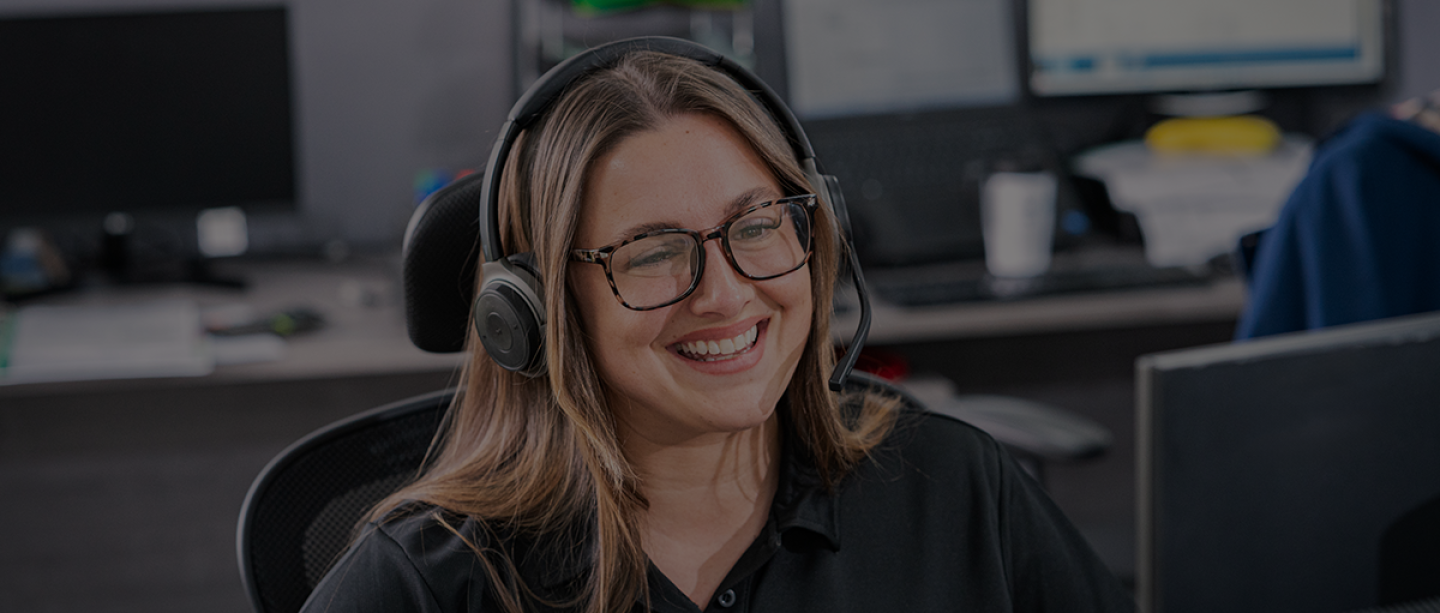
Contact us
Our global teams are ready to provide the support you need